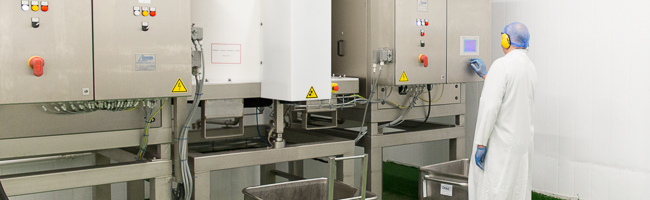 |
Food often needs chilling at the beginning of or during the production process. For this type of cooling ice is extremely effective; used as an ingredient, it chills precisely where it has the most immediate impact. Whether its in dough, where low temperatures are needed to ensure the correct elasticity and development or meat to prevent heat build up during chopping / grinding operations.
Ice can also be used during the immersion cooling stages in cook and chill operations to aid rapid post cook chilling, controlling the water bath temperature and absorbing the excess heat from the product to maximise the cooling rate. The water acts as a rapid heat conductor while the ice acts as a thermal battery.
Dosing
For any operation however ice must be dosed into the product / cooling vessel in controlled amounts. In small operations this is usually done by weighing the ice and adding it by hand. However is a large operation this is not always practical, so the ice must be delivered to the process and dosed automatically, accurately and repeatably.
Ziegra Solutions
Below are some of the bespoke solutions that Ziegra have designed over the years to achieve ice dosing. The ice can either be pre-dosed into a cart or other container for adding to the product later, or dosed directly into the processing equipment, depending on the demands of the application. All of our systems are intrinsically hygienic and also have Hygiene + options to meet even the most demanding specifications.
|
|
|
|
The system on the right consists of a UBE 3.500-2 granular flake ice production unit next to an AS 500 mini silo which are mounted on the production floor. The ice machine is a special vertical construction with ice maker section mounted above the refrigeration section. This helps to bring the ice discharge to a more convenient height for feeding the silo and to reduce the footprint of the plant. The idea with this system is that a mobile dough mixer bowl or euro cart is brought to the plant, the required quantity of ice is entered into the control panel, then the correct amount of ice is dosed into the mixer bowl / cart.
The units shown to the right of the plant are remote weatherproof condensers to be located outside. This unit could also be used to supply smaller quantities of ice into small containers for manually adding to the mix. |
|
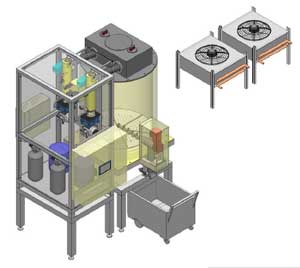 |
|
|
Above: Dosing granular flake. Method 1 |
|
|
|
Once the ice has been dosed into the container or cart it is then ready for loading into the next process stage. Carts are usually hoisted mechanically, while smaller quantities are usually added manually. |
|
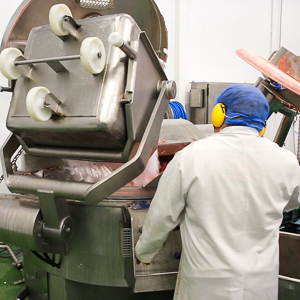 |
|
|
|
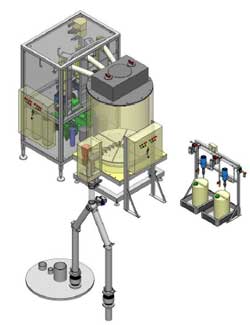 |
|
The system on the left consists of a UBE 7.500-2 next to an AS 500 mini silo. Again the ice machine has a special vertical construction with the ice maker above the refrigeration system to give a smaller footprint. It is a similar idea to the one above, however in this scenario the plant is situated directly above a process. The plant could be controlled from the prodcution floor via a remote HMI, or a signal could be sent via a process control system to the plant to let it know when / how much ice to dose. Up to two units can be dosed one at a time with this plant. The ice is extracted automatically then fed by gravity to the application below.
The small unit sitting to the right of the ice plant is a Hygiene+: Cleaning and dosing system.
|
Above: Dosing granular flake. Method 2. |
|
|
|
|
|
The system on the right shows 3 x UBE 7.500 ice machines next to an AS 1.000 mini ice silo. This system is operationally identical to the scenario described above, with the only difference being that a transverse screw conveyor is shifting the ice horizontally before is is dropped by gravity into the process below. This is for applications where the plant is mounted above, but offset to the process. |
|
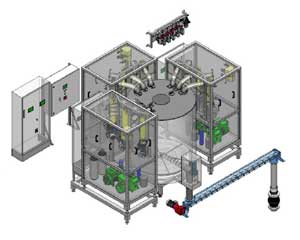 |
|
|
Above: Dosing granular flake. Method 2 offset |
|
|
|
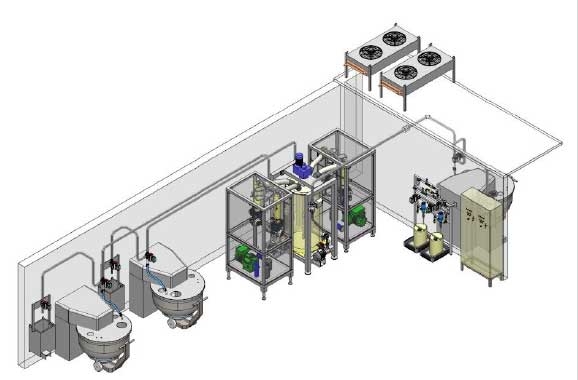 |
|
Where there is no space above the point of use for method 2, an SIF system like that shown on the left can be used, which uses a liquid pumpable freshwater ice. This plant can be remotely situated on the same level as the mixer / chopper / immersion tank and the ice pumped up to 60metres to where it is needed. An SIF system can be designed to feed multiple points of use, either one at a time or simultaneously. While not as energy dense as granular flake, it is usually enough for all but the most demanding operations. |
Above: Pumpable StreamIce: Method 3 |
|
|
|
|
|
The plants above are just examples of those we have designed over the years, if you have a process that would benefit from powerful, accurate and reapeatable cooling please contact us to discuss a Ziegra dosing system. |
|
|
|
|
|
|